Preventing Boiler Explosions with Proper Maintenance
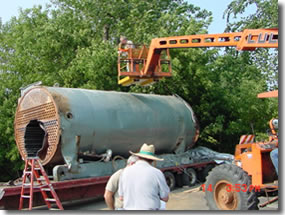
This boiler failed because of improper
water conditioning
Low pressure boilers are commonly used for institutions and apartment complexes. The water resides OUTSIDE of the tubes while the hot gas traverses inside the tubes. The tubes are supported by two identical tubesheets similar to the one shown in the figure on the left.
Low water failure is a leading cause (75% of the cases) of boiler failure, but is not the only reason. Low water usually results in overheating and loosening of tubes, collapse of furnaces and in complete destruction of boilers. Symptoms of low water operations can be detected and avoided before catastrophe by proper maintenance procedures.
Generally, boiler failures are a result of sloppy maintenance and operational procedures such as:
- Frequent shutdown-startup (cycling) that can lead to thermal fatigue.
- Inadequate blowdown which results in sludge accumulation and scale buildup.
- Faulty water treatment resulting in increased concentrations of dissolved. sodium that leads to caustic cracking particularly in weld-zones.
- Lack of proper water de-aeration which results in accelerated corrosion and attendant thinning of the steel shell, tubing, and tubesheets including stress corrosion and crevice corrosion of welded joints.
- Poor maintenance of safety relief valves resulting in sticking of valves and bad setting of safety valve valves.
- Poor maintenance of automatic control systems such as water level monitors.